While Tom and I were at Cumberland Gap National Historical Park, we had the opportunity to tour JR Hoe and Sons Iron Foundry. Tom had been doing the Iron Furnace talk and was interested in finding out more about the iron heritage in Middlesboro. Middlesboro was founded as an iron town, “The Pittsburgh of the South,” although it didn’t stay an iron town for long.
But this beginning attracted JR Hoe, an ironworker from Pittsburgh. JR took over the Pioneer Iron Works in 1909. He soon changed the name to his own. Over time, his five sons developed the company into a regional center of metalworking expertise. By the mid-20th century, the company began diversifying into construction products, becoming a major supplier of manhole covers. Since the 1980’s, JR Hoe has further expanding into industrial and architectural castings.
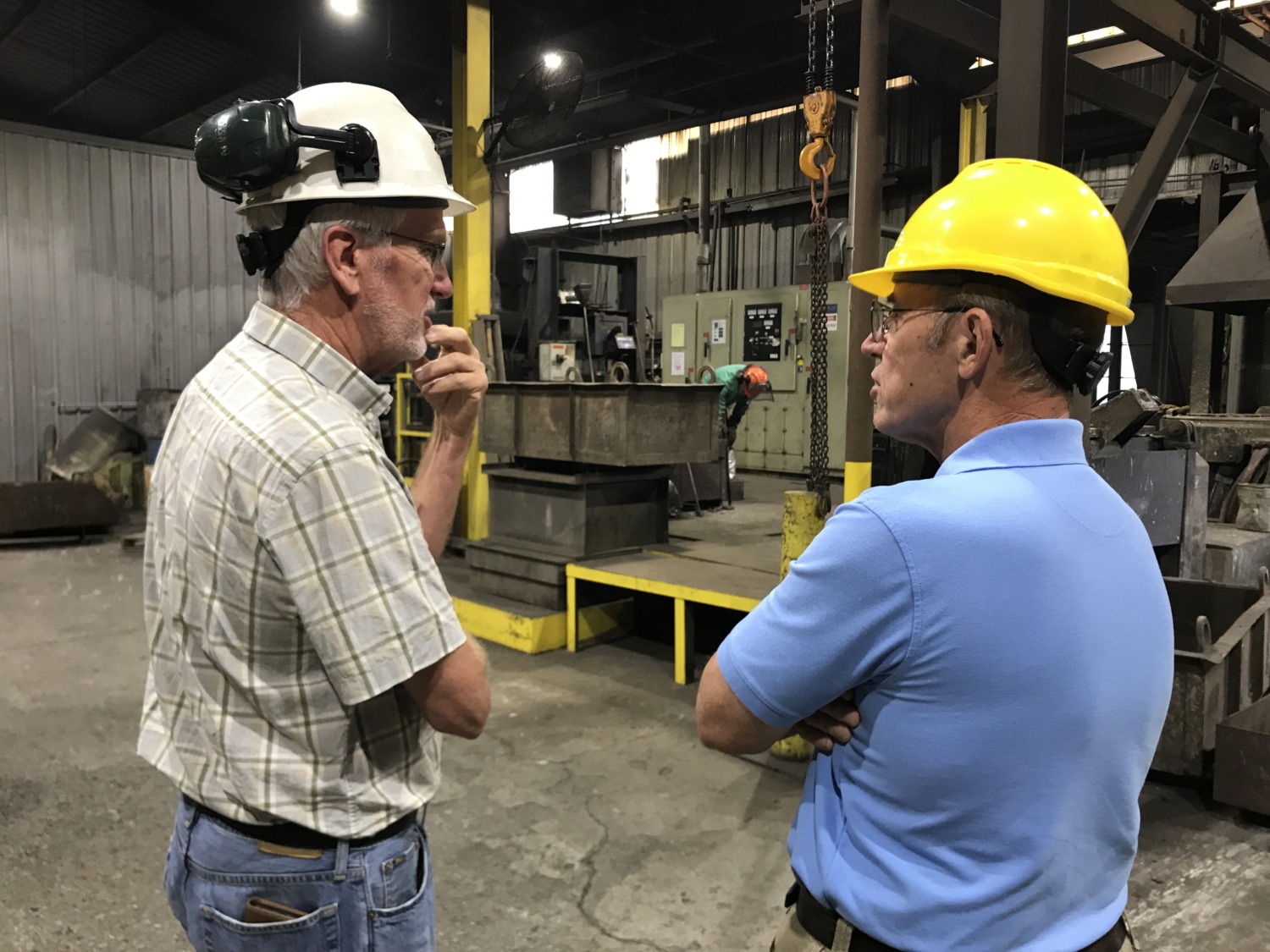
Today, JR Hoe is still family owned and operated. The President of the company is HH “Bo” Hoe. He has worked at the company since 1979 and is the fourth generation Hoe to sit at the helm. His two sons also work for the company. Chuck Blank introduced us to Bo at the Levitt Concerts. Bo is the Chairperson for the Levitt Concert series and is very involved in the community. Bo invited us to tour the foundry but asked that we wait until the concert series was over.
On a cooler day in September, we drove to the JR Hoe Iron Foundry just off Cumberland Avenue in Middlesboro. We met Chuck and one other person there and were given a personal tour by Bo.
Seeing the company and how it works was very impressive. We were able to watch all the steps in making iron castings. From putting the molds together, to pouring the iron, to taking the product out of the castings, and the finished, polished product. Of course, the most interesting thing was watching them pour the molten iron. Safety is a very high priority at the foundry.
Bo also showed us the place where they make the molds. The company is investing in laser cutters to make the molds more precisely. Recently the company has expanded into architectural bollards for passive safety measures at government buildings. They look good and deter reckless drivers. Manhole covers are still a big part of the foundry’s business.
Bo talked to us about the challenges faced by a small foundry. They don’t have the efficiency of scale of the big iron foundries, but they are able to give better customer support. JR Hoe can even make one-of-a-kind castings although those castings can be very expensive. Bo said it is a fine line between keeping their items affordable and being able to make a profit in the business. I don’t think anyone in the family is getting rich but they are able to employ about 70 people in their foundry. Very valuable in the community.
We really enjoyed our tour of the JR Hoe and Sons Iron Foundry. I learned a lot about some things I don’t usually think about. I was especially impressed with how the company recycles all their materials. Thanks to Chuck for setting it up and to Bo for taking the time to show us around.